ZM3211 Industrial 4.0 Training System Didactic Equipment Mechatronics Training Equipment
1 Equipment introduction
1.1 Overview
The modular flexible manufacturing production line training system is a typical mechatronics and automation product. It is specially developed for vocational schools and education and training institutions.It is suitable for teaching and training in mechanical manufacturing and automation, mechatronics, electrical engineering and automation, control engineering, measurement and automation, control technology, computer control, automatic control and other related majors.Close to the industrial production and manufacturing site, it is specially designed for practical training and teaching, strengthening various control and engineering practice capabilities.
The system includes 4 stations, namely distribution system, loading and unloading station, assembly station, and sorting and warehousing station. The control system uses Siemens S7-1200, which has good flexibility capabilities. Each station has an independent PLC. Control system, each station can operate independently or jointly with two nearby stations, three stations... or four stations. Students learn the design, installation, programming, debugging, and complete machine training and operation of complex systems. The system includes mechatronics pneumatics, motor drive and control, PLC, sensors and other control technologies, and is suitable for students to carry out engineering practice, course design and junior engineering technology engineer training.
1.2 Features
(1) The training platform uses an aluminum alloy platform with universal wheels installed at the bottom. Two lockable wheels can be flexibly moved and fixed anywhere.
(2) The I/O terminals of the PLC module of the main station and sub-station of the training and assessment device are connected to each command switch, photoelectric switch, sensor and indicating element through the terminal block; each actuator module is placed on the base plate, which is easy to use and Not easily damaged; the PLC control unit is installed in the training cabinet, safe and reliable.
(3) The system organically integrates machinery, pneumatics, electronic control, motor drive, sensor detection, PLC and industrial control network technology. It has a modular structure and is easy to assemble. It can complete various single skill training and comprehensive training projects. It can undertake the installation and debugging of mechanical parts, pneumatic system installation and debugging, electrical control circuit installation and PLC programming, electromechanical equipment installation and debugging, automatic control system installation and debugging, industrial network control system installation and debugging, and can well meet the needs of practical teaching and engineering training. need.
(4) Both the mechanical structure and the control system adopt unified standard interfaces, which have high compatibility and scalability. With the rapid development of industrial technology, the system follows the on-site technology upgrade and expansion to further meet customer needs and practical teaching; This system cultivates learners' thinking and abilities. Learners can use this system to learn from mechanical assembly, electrical design, wiring, PLC programming and debugging, fieldbus form engineering training and maintenance, etc.
2 Technical parameters
Input power: single-phase three-wire 220V±10%, 50Hz
Size: about 700mmx800mmx1400mm (maximum size of a single unit)
Capacity: <1KVA
Weight: <100Kg (weight per station)
Ambient temperature: -10℃~+40℃
Relative humidity: <85% (25℃)
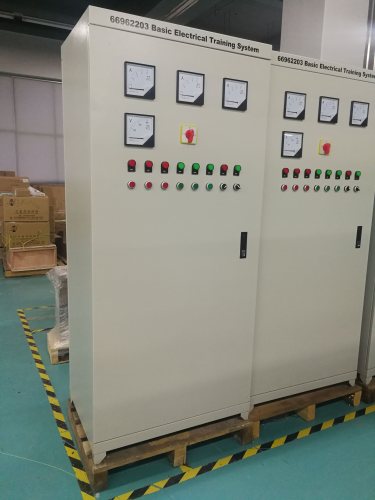
4. Experiment list
Experiment 1 One-stop stand-alone test experiment
Experiment 2 Two-station stand-alone test experiment
Experiment 3 three-station stand-alone test experiment
Experiment 4 Four-station stand-alone test experiment
Experiment 5 Equipment Online Test Experiment
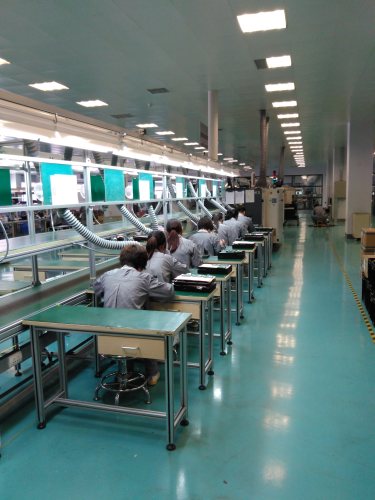