SR-WL900 Steady-State and Non-Steady-State Heat Conduction Fluid Mechanics Experiment Equipment Eduicational Equipment
Description
Heat conduction is the transport of heat between the individual molecules in solid, liquid and gaseous media under the influence of a temperature difference. Steady heat conduction is the term used when heat transport is maintained permanently and uniformly by adding heat. In transient heat conduction, the temperature distribution in the body is dependent on location and time.
Thermal conductivity λ is a temperature-dependent property of a material that indicates how well the heat propagates from a point in the material.
WL 900 can be used to study both steady and transient heat conduction. The trainer consists of a heat source and a heat sink, between which cylindrical samples made of different metals are inserted. Each sample is fitted with 12 temperature measurement points. The temperature measurement points are designed to has as little influence on the temperature as possible and the core temperature of the sample is measured.
The heat source consists of an electrically heated hot water circuit. An electronic controller ensures the heating water is kept at a constant temperature. The heat sink is realised by means of a water cooling system. An elevated tank ensures a constant cooling water flow rate.
A temperature jump can be generated by appropriate regulation of the cooling water flow. A PC can be used to display the transient temperature distribution in the sample over time and place. Our price didn’t contain PC.
The temperatures of the sample, heating and cooling water, as well as the electrical heating power and the cooling water flow rate are displayed digitally on the switch cabinet and can be transmitted simultaneously via USB directly to a PC where they can be analysed using the software included. The thermal conductivity λ can be calculated from the measured data.
Technical details
Specification
investigation of steady and transient heat conduction in metals
determining the thermal conductivity λ
heating water circuit as heat source, electronically regulated
electric heater with PID controller
elevated tank with overflow for generating a constant cooling water flow rate
samples made of 5 different metals
cooling water temperature and flow rate measurement
digital displays: electric heating power, temperatures, cooling water flow rate
software for data acquisition via USB under Windows 7, 8.1, 10
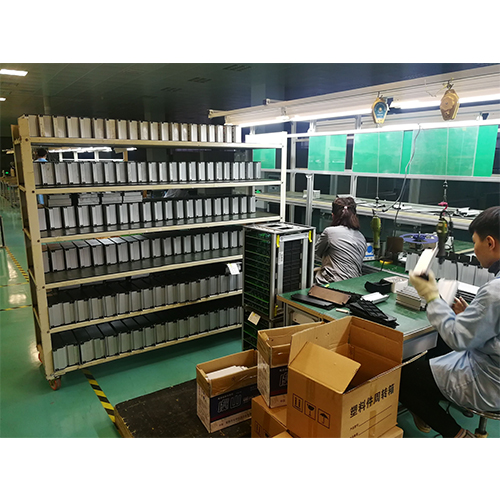
Technical data
Heater
output: 800W
temperature: 20…85°C
Samples, Ø 40mm
3x 450mm (copper, aluminium, brass)
2x 300mm (steel, stainless steel)
Heating tank: ca. 2L
Cooling tank: ca. 0,5L
Elevated tank: ca. 6L
Temperature sensors
12x thermocouple type K, along the sample
2x Pt100, in the cooling water
1x Pt100, in the heating water
Measuring ranges
temperature: 14x 0…100°C
power: 0…1000W
flow rate: 0,1…2,5L/min
230V, 50Hz, 1 phase
230V, 60Hz, 1 phase, 120V, 60Hz, 1 phase
UL/CSA optional